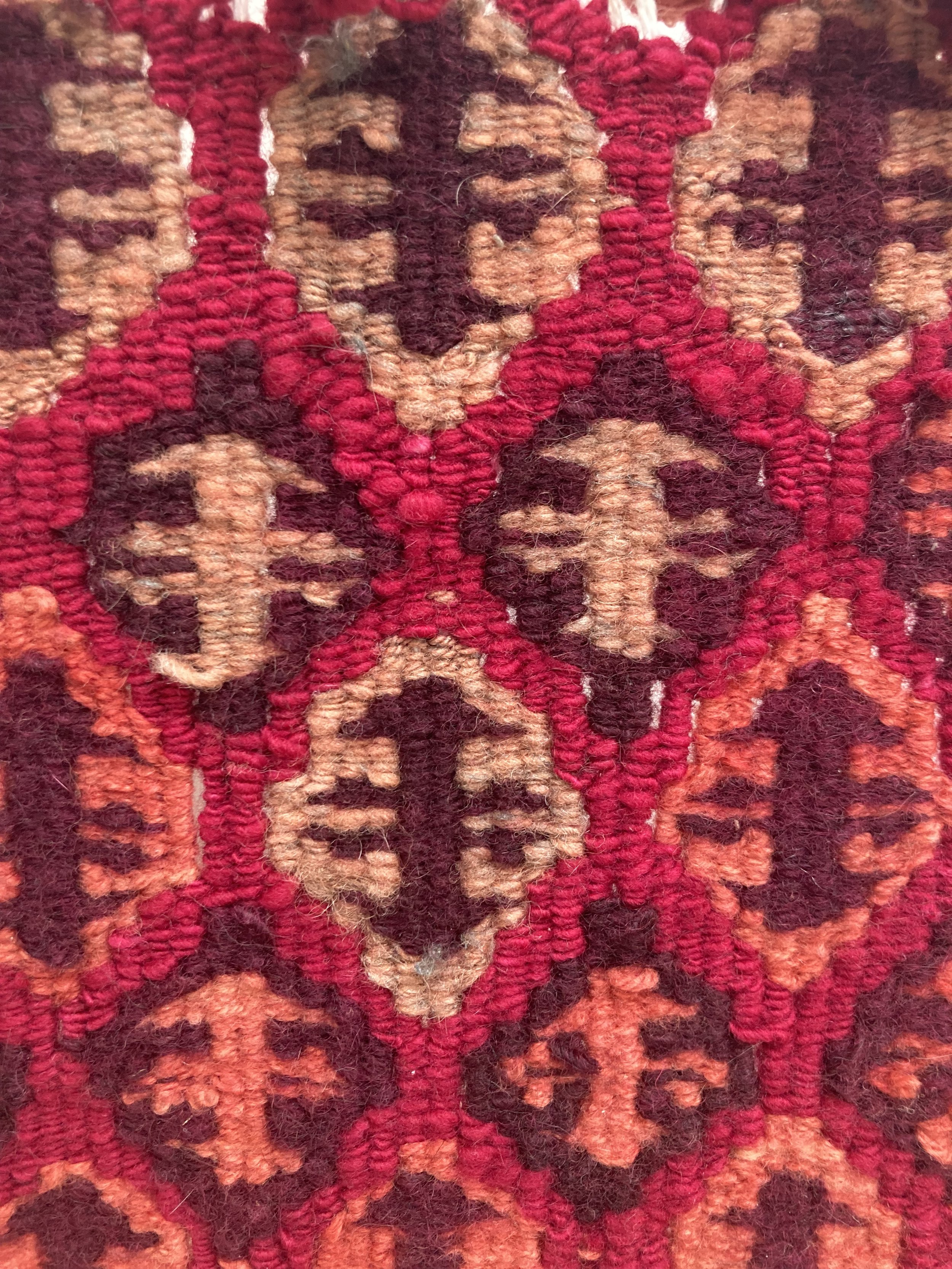
MIDI Rug
a continuing experiment in electronic textiles
How does culture influence technology?
We often think of technology as sterile, western, all hard metal and void of culture, Weaving is typically considered an archaic practice, despite its impact on our modern society. The first computer was actually weaving loom; it used punchcards that would determine the pattern of fabric. After I was exposed to electronic textiles made by people like Ebru Kurbak, I was interested in connecting my weaving practice, interest in Assyrian textiles, and tech, to making a conductive rug. This is my process making a MIDI board in the form of a kilim, or flat-woven rug from scratch.
Materials:
Cotton warp
Hand-spun and naturally dyed wool (pomegranate & cochineal)
Steel wool and conductive thread
Stranded insulated wire
Snaps and other attaching mechanisms
Arduino Pro Micro
9.1M Resistors
Beads for temporary exposed wire insulation and decoration
Wood scraps made into a simple deconstructable tapestry loom
30” x 30”
2023
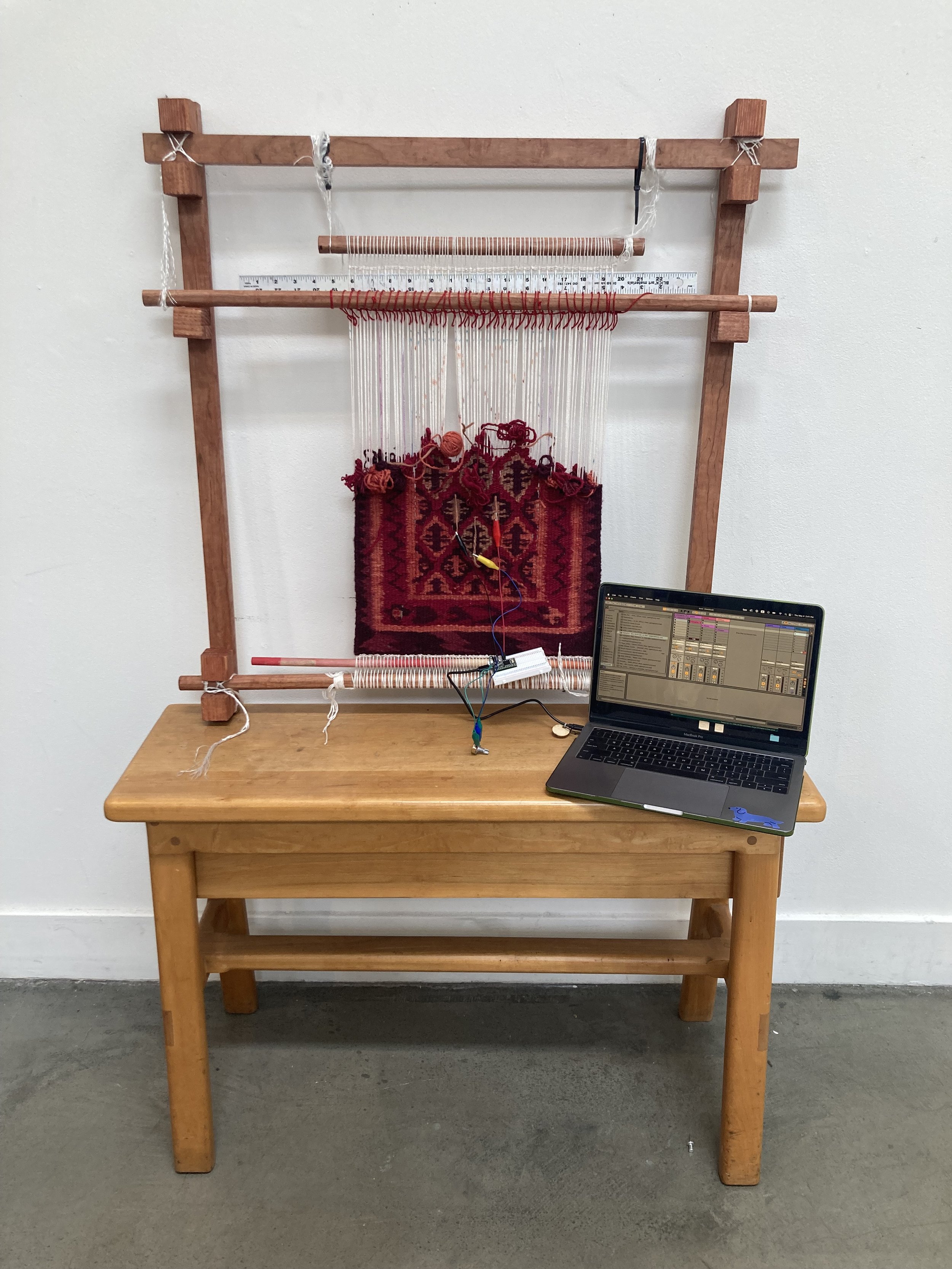
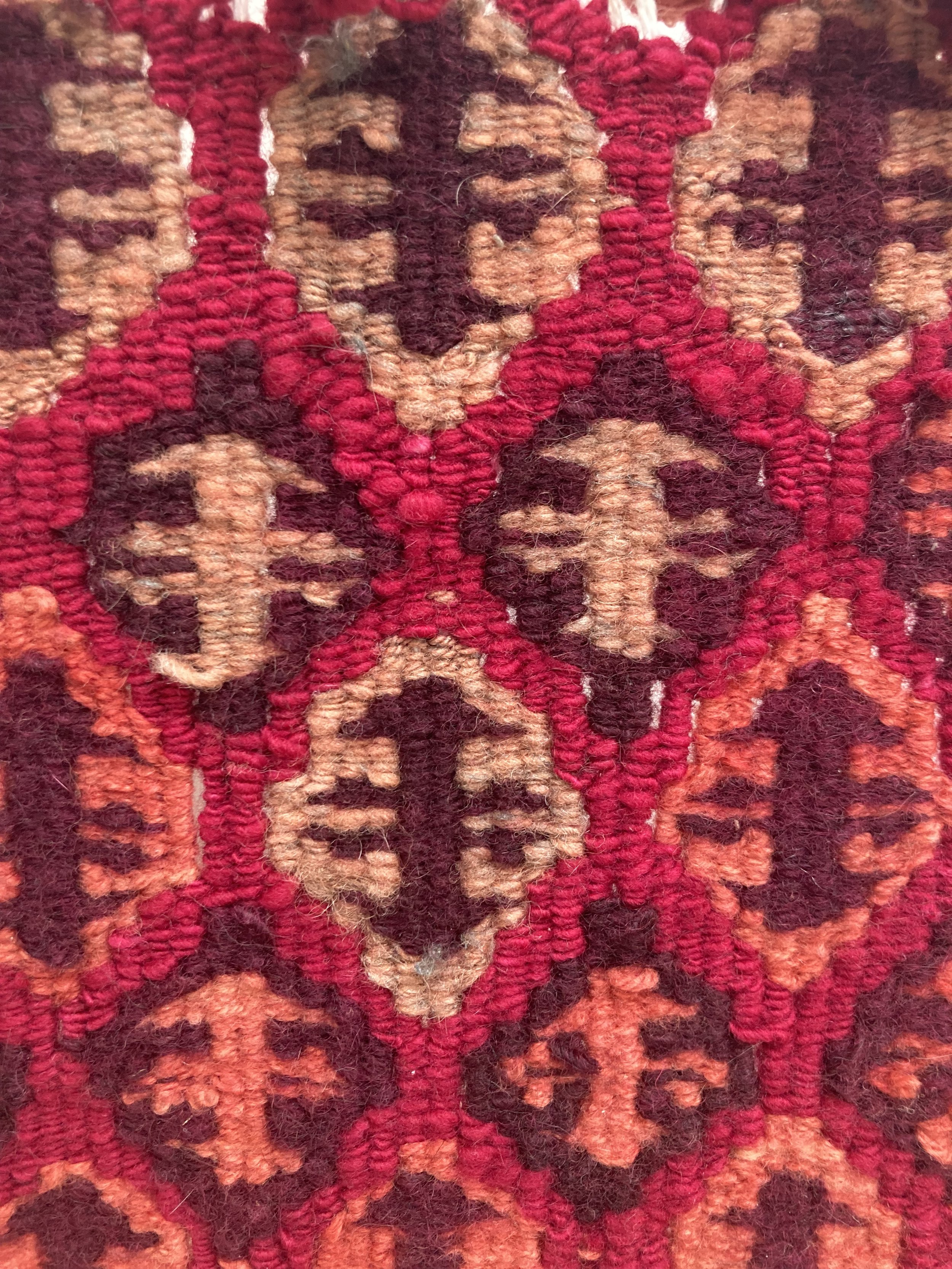
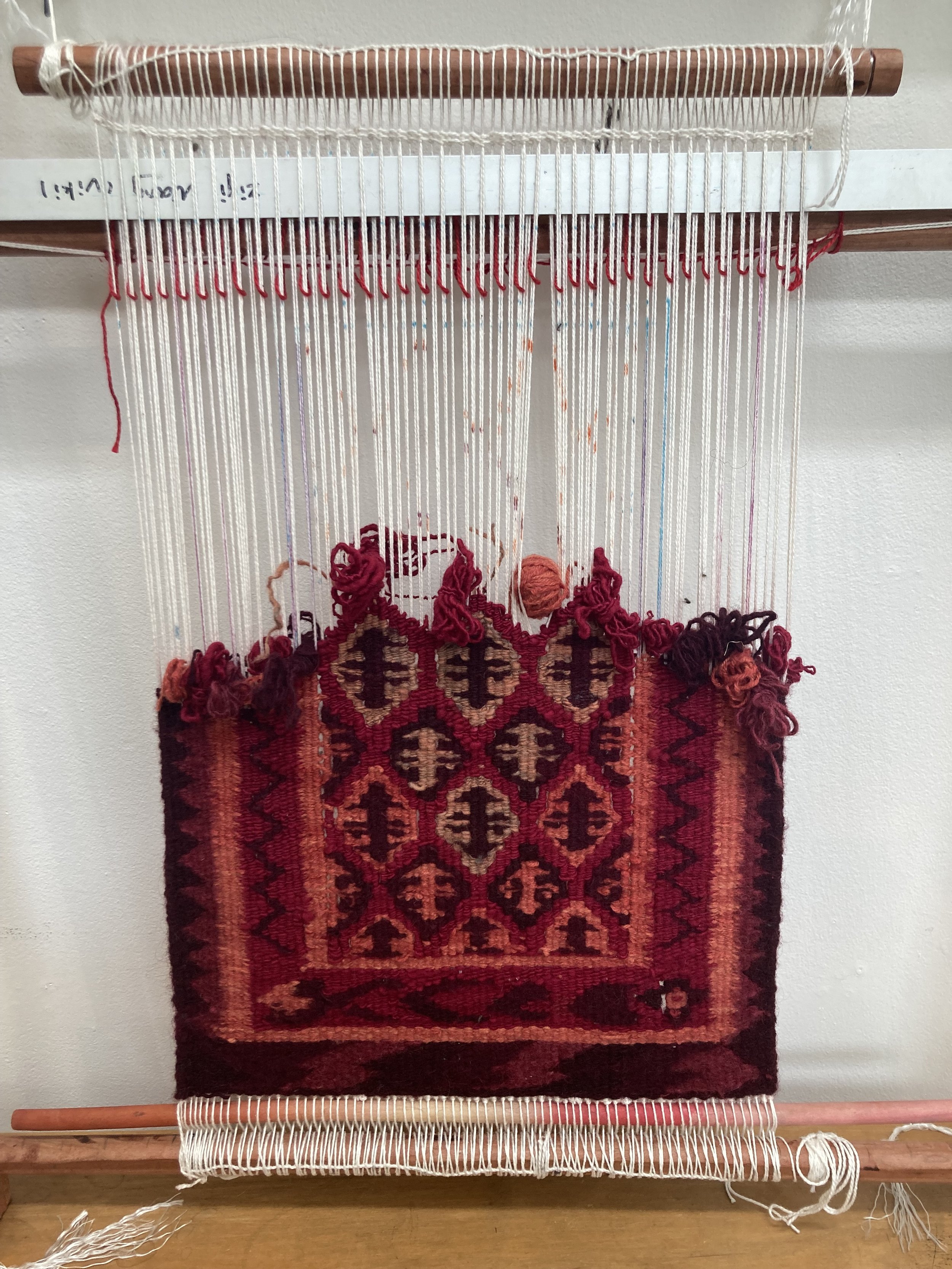
Each tan colored patch of weaving is conductive. When someone or something else conductive touches it, the computer is notified, and MIDI note is sent to whatever audio or video program I’m using. I can map those different notes to trigger sounds or actions, like an electronic keyboard or drumpad.
Process
Ideation & Experimentation
Goal: Make a handwoven flatweave (aka kilim) rug MIDI drum pad/keyboard that audience members can touch in different places to create/affect music.
Diagram for making the loom
1st prototype: string heddle loom make out of chopsticks. Tried making a "button" out of two pieces of conductive fabric separated by a piece of a sponge with holes in it, hooked up to a battery and a light. When you squished it down, the two pieces would connect and light the LED. Cons: too clunky to weave in.
2nd Try: Instead of a button, I used two woven patches of conductive thread. When I touched both patches at the same time, my bodies conductivity would connect the circuit. Cons: Very unreliable, had to lick my finger to increase conductivity.
2nd Prototype: A woven strip of fabric I inlaid with conductive thread in a series of squares. Using capacitive touch (the same tech that allows your smartphone to know where your finger is in the screen) I could more reliably send signals over to use for my MIDI board.
Spinning the Wool
I washed and carded the wool, which is like brushing or combing it so all the fibers run in the same direction.
To make the conductive yarn, I blended (aka carded) the steel wool fiber with the wool roving as evenly as I could.
Then, I used a drop spindle and a spinning wheel to spin it into yarn.
Carding the regular and steel wool together
Close up of steel wool and regular wool roving carded together
Spinning using a drop spindle, I am getting the hang of it!
Dyeing the Yarn
First, I mordanted all my yarn with pomegranate, which are full of tannins. When you make a very strong “tea” out of the rinds and simmer your yarn in it for a while, the bath gets it ready to accept your dye at the molecular level.
Then, I ground my cochineal (very small bugs) and boiled it into a dye bath to simmer more of my yarn.
Finally, I soaked some of my dyed yarn in a post mordant bath made of iron and warm water to get a darker color.
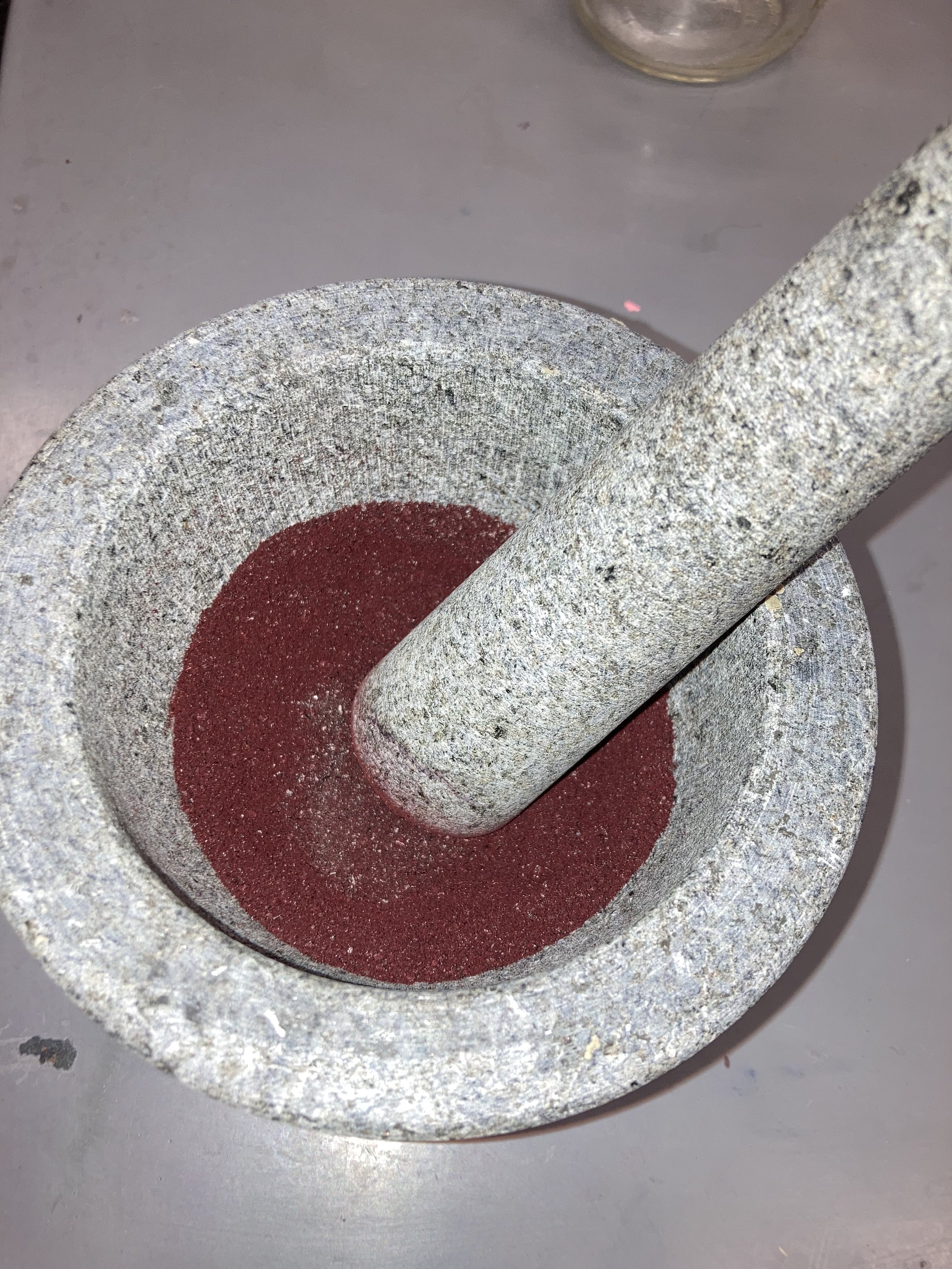
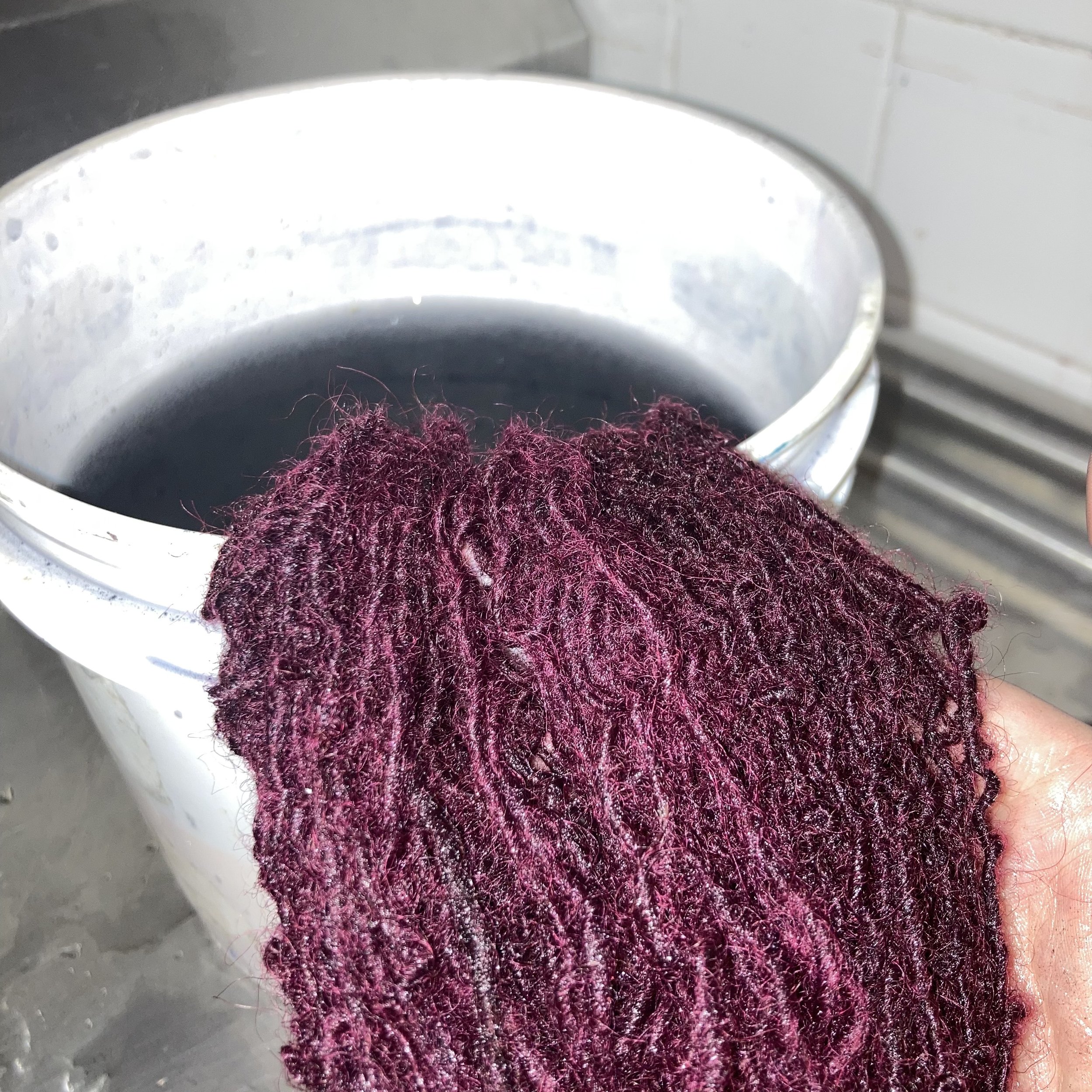
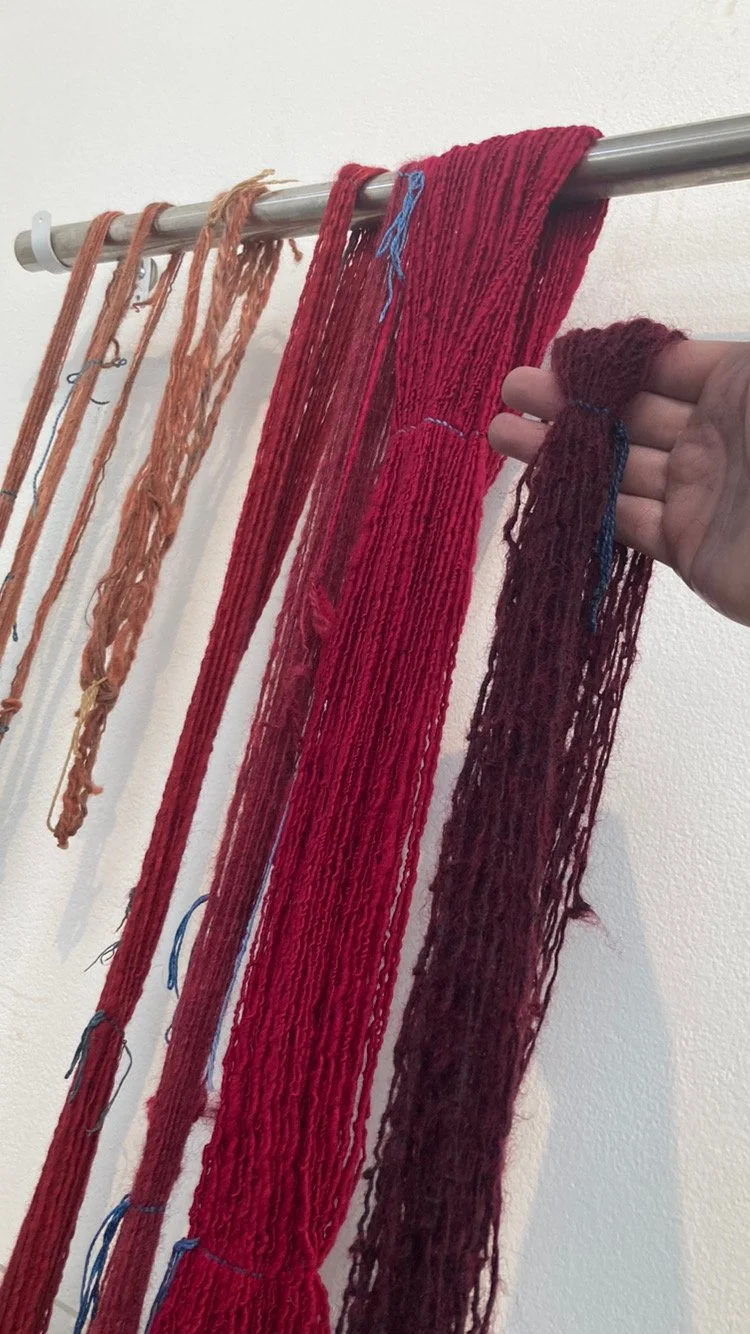
Weaving
After I made my loom, I wound my warp. This got all my threads in order so I could start to weave. Then, following my drawn diagram aka “cartoon” I wove my design.
These strings are my heddles, they keep 1/2 of my warp up so I can weave back and forth easily.
To Be Continued…
Here’s some in progress shots for upcoming updates!
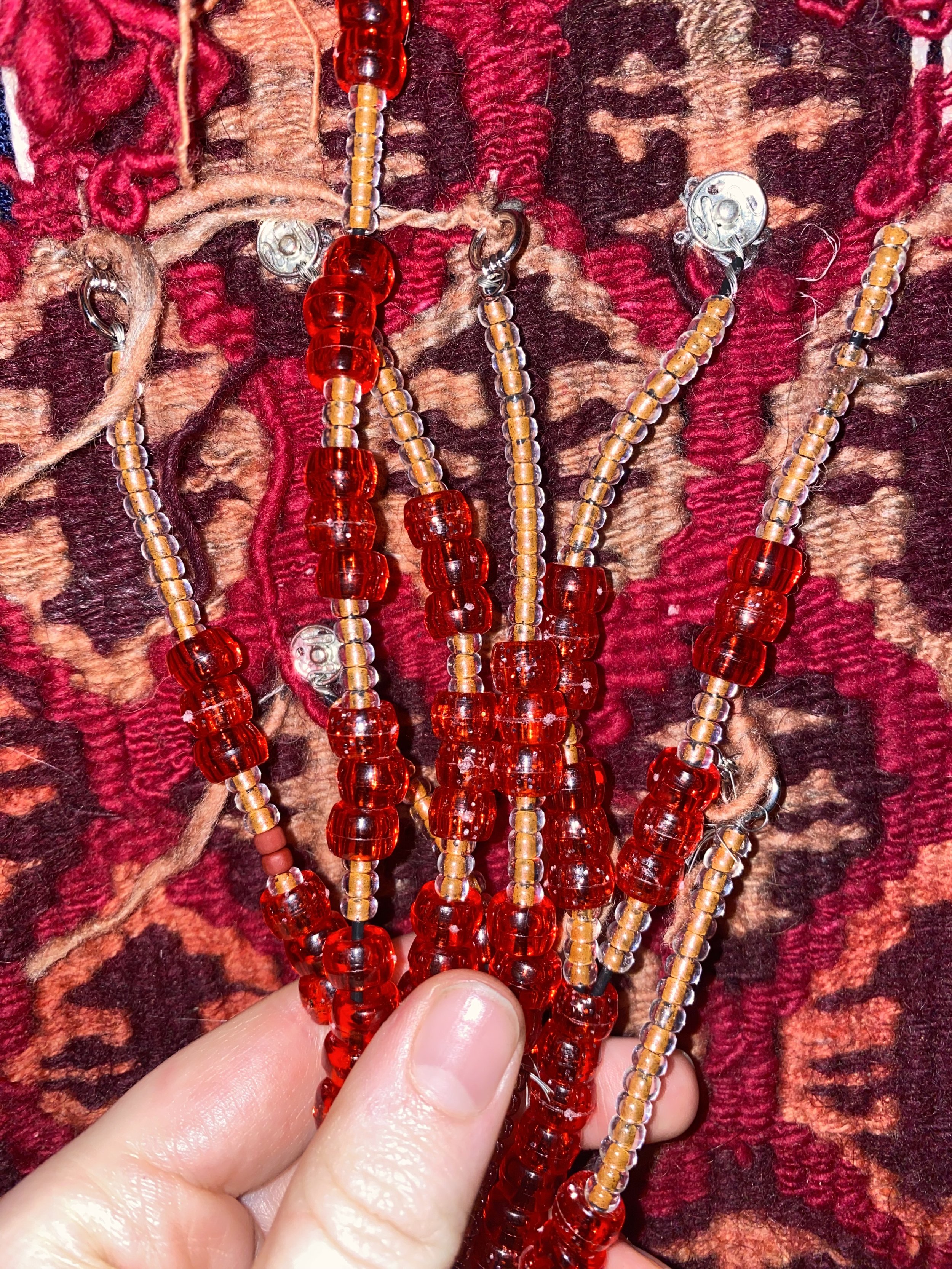
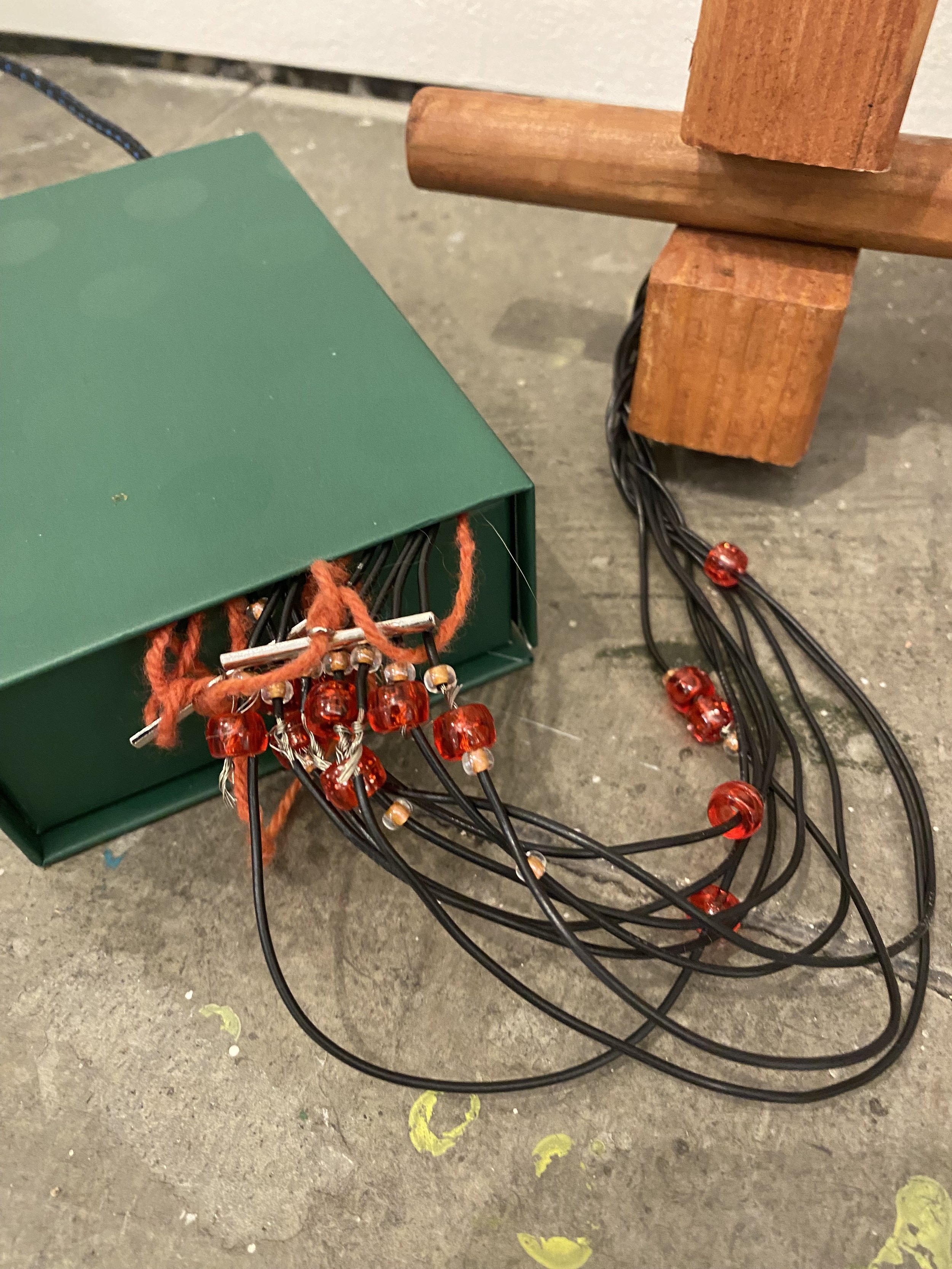